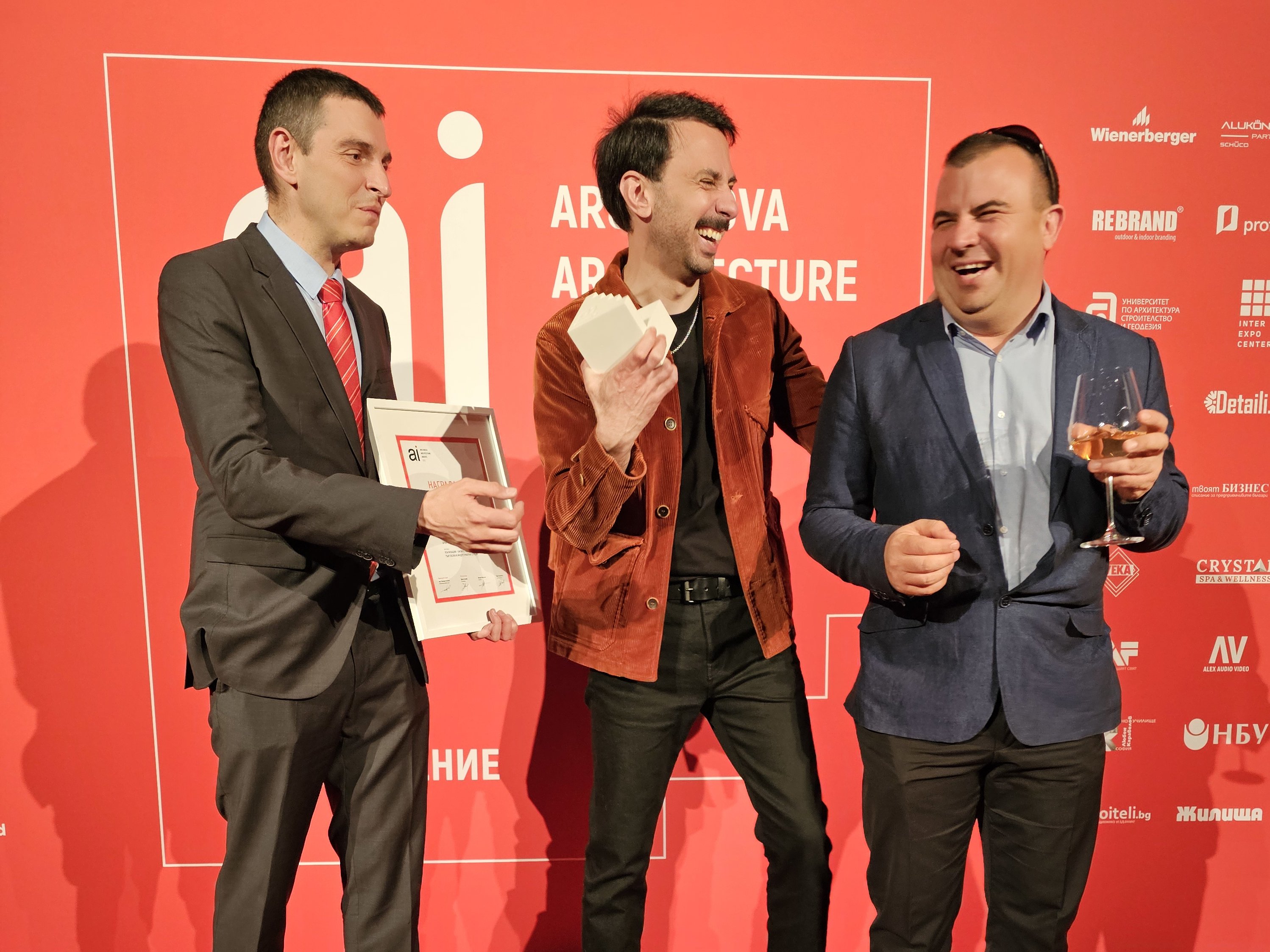
The High-Tech Melexis Building wins 2023 Archinova architectural awards!
IPS Bulgaria wins another accolade! In the competition which puts quality architecture in the spotlight – Melexis Extension Building project in Sofia won in the category "Realizations - Business, admin, commercial and industrial buildings."
Melexis's motto is “Innovation with heart,” and the project boldly represents this. It has already won the 2022 Building of the Year Award for Industrial Buildings and Green Industrial Buildings.
Group-IPS leading the design phase
IPS Bulgaria's in-house design team with arch. Maxim Mokdad led the design phase, collaborating with Melexis’ architect based in Belgium – arch. Sebastian Mortelmans, Mortelmans Van Tricht Architects.
Various options were carefully assessed and evaluated, resulting in innovative solutions such as rainwater collection, recycling, and installing the most extensive single-volume gas sprinkler system worldwide. Emphasis was placed on creating a comfortable work environment with direct access to green spaces and ample natural light.
Apart from design, the IPS team also served as Project Manager and handled urban planning procedures on behalf of Melexis Bulgaria.
About Archinova Architecture Awards
For the 10th year, the competition puts quality architecture in the spotlight. It encourages valuable projects with bold and innovative ideas, gives way to the expression of talent and intellect, defends high quality and values, seeks the cherished balance between investment and idea, and evaluates the merits of each work impartially and honestly.
It distinguishes sustainable, functional, and beautiful architecture with a view to the future. Still, it does not give up the lessons of the past in timeless architectural examples; the competition focuses on your achievements.
The "ARCHINOVA ARCHITECTURE AWARDS" awarding ceremony is a long-awaited event for the architectural college and construction industry representatives. The nominations are presented during the event, followed by an award ceremony.
Investment characteristics of the building:
Melexis designs, develops, and delivers innovative solutions in the field of microelectronics. Given the increasing need for chips worldwide, as well as the company's growth plans, in 2022, Melexis completed its new production and administrative building in Sofia. It complements the current complex and increases the production areas, warehouse base, research and development activity.
The new building is divided into two parts - office and production. She will contribute to Melexis' future growth in both new product development and increased chip testing capacity in production. The newly built building has a capacity of 250 workplaces in the office part, and more than 450 machines can be located in production with the new part. The increased capacity led to the creation of 160 new jobs.
With its new production and administrative building, Melexis applies high standards for the quality of the working environment. The project's main objective is to expand the company's production capacity, avoiding the segregation of employee flows by centralizing the approach and social functions in the building. The building has an expanded area of 16,000 sq.m., divided into three levels. On the first floor of an area of 6,630 sq.m., production, storage, and technical premises serve the production activity.
Modern office spaces are located on the second and third floors of an area of 9,330 sq.m., providing various opportunities for work and rest. On the second floor are also the dynamic areas in the building such as reception and meeting rooms. There is also the recreation and dining area, as well as the dressing rooms of the production team and the second level of the warehouse. The new production is currently the largest for the company's microchip test.
Architecture, design, functionality:
The building is located in the capital's Gorublyane district, fitting organically into the urban environment. It is a project with many innovations and technical achievements. The gas extinguishing system ranks among the largest in the world, and challenges in terms of tightness in such large spaces accompanied its implementation.
In addition to the standard for every building's electrical, plumbing, and ventilation installations, the building has specific systems providing natural gas, compressed air, liquid nitrogen, and propylene glycol for the needs of the production process. The highest level of fire resistance is ensured through automatic fire doors, curtains, and a gas extinguishing system. The specificity of the production process of electronic components imposes high requirements on the architectural and finishing works in the production premises.
The flooring is an integrated ESD system for protection against static electricity, and the unique installation of the suspended ceiling (Tate Grid) allows quick, easy, and, above all, clean installation of all the systems required for production. Integrated vertical racks in the warehouse, used to store chips and packaging materials with a height of 10 meters each, help optimize space in height.
The office premises on the third floor occupy only part of the floor area. The remaining areas are distributed between a technical roof, surrounded by high facades to ensure the integrity of the volumetric composition of the building, where technological HVAC equipment is located on an additional steel platform with an area of 900 square meters and a landscaped roof terrace.
Green areas are integral to the vision for providing employees with a comfortable and greener environment. The building has 5 Japanese patios - each with an area of 70 m² and two landscaped terraces. The project implements a new internal road network, parking area, allocation of 6 decares of accessible park area, new crossing point with covered bicycle parking, etc. The park zone and the rich landscaping of the territory create a natural natural framework.
Construction, energy efficiency, and technological indicators:
The wide range of functionalities and high requirements necessitated combining various innovative and non-standard structural and architectural solutions, construction technologies, and installations characteristic of different types of buildings – industrial, office, and public.
Carrying out the project during the nearly two-year global pandemic presented challenges to Melexis and the designers and contractors. The construction of the building is combined, combining all the main types of construction - monolithic reinforced concrete, fiber-reinforced floor slab, a prefabricated-monolithic system of the "Spiral" type, classic steel construction, as well as combined steel-reinforced concrete elements. The volumetric composition avoids the usual one-volume solutions for production buildings, achieving a harmonious balance of two- and three-story volumes.
The facade solution is minimalistic, modern, and without unnecessary decoration. The solid parts are solved with metal sandwich panels, on which a sheathing of cut decorative sheet metal is mounted, giving detail and a sense of depth to the finished facade. The grass area of the grounds is 11,000 m², divided into zones that special lanes can reach.
Technologies ensuring sustainability in the use of natural resources are applied. On the first floor of the building is the compressor room with compressors and dryers necessary for the production process. The heat released from them is used to heat the building, as well as to heat water for domestic needs. This process reduces the use of resources such as gas and electricity. A tank was built to collect rainwater and use it to power the toilets. The building has a hall for sports activities with changing rooms, lockers, and showers for the convenience of employees.
The entire building is managed centrally with a unique Building Management System (BMS) for Bulgaria, which was developed according to Melexis' needs with preset efficiency settings and scenarios for specific situations. BMS monitors the air conditioning, lighting, external blinds, fire alarm and fire extinguishing, elevators, compressor room, heating, humidity, and video surveillance systems around the clock. The BMS maintains the set lighting and heating levels, saving energy and not consuming unnecessary resources.
On the territory, there is a parking lot for 168 cars with five separate charging stations for electric vehicles. A controlled access area can accommodate 40 bicycles and 16 motorcycles, with six charging points for electric bicycles and motorcycles.